Bringing Your Product to Life with Custom Nameplates and Branding
Branding is identifying your product as yours and creating a distinct look and feel during the user experience.
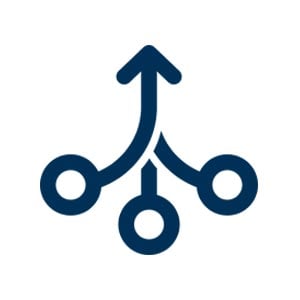
One-stop Shop
A multitude of nameplate options and vertically integrated capabilities enable Boyd to incorporate custom nameplates into user interfaces, enclosures, and more.
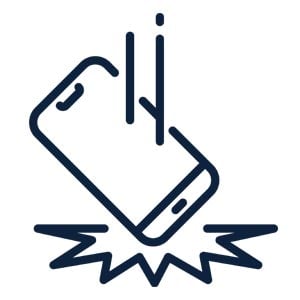
Improved Durability and Lifetimes
Leverage durable branding solutions from Boyd to help protect products from harsh usage conditions and environments.
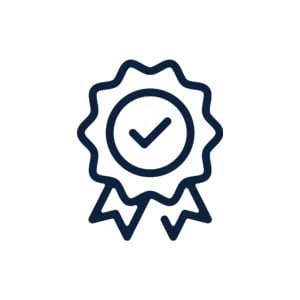
Meet or Exceed Exacting Standards
Leverage Boyds capabilities to produce branding, signage, or decals that meet stringent requirements for automotive, aerospace or consumer applications.
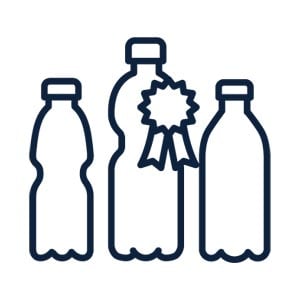
Differentiate Your Product
Stand out from the competition with quality consistent, exacting parts for distinct, stand-out product identification that meet your product vision.
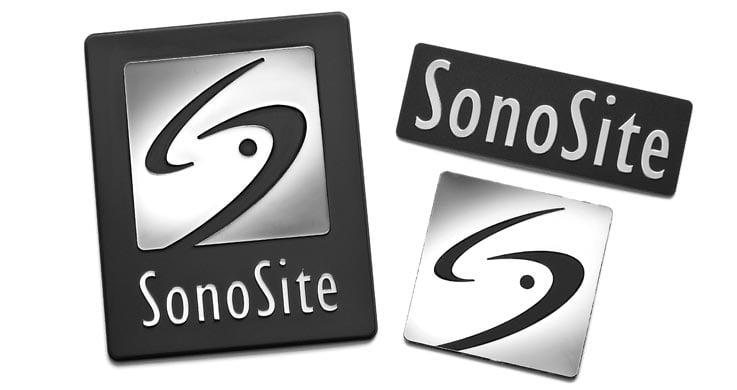
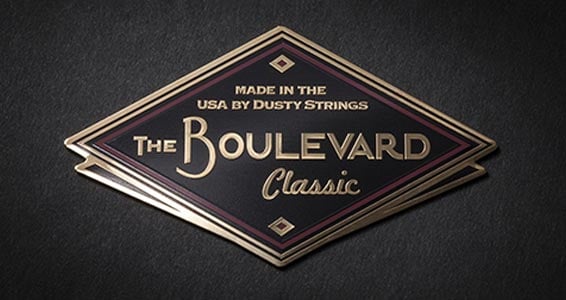
Custom Nameplates
Boyd’s exceptional design support, color-matching, and fabrication methods bring custom product nameplates or badging to life, visually representing your brand in a way that differentiates your company and products. Every custom-made nameplate meets each customer’s specific needs and is adapted to withstand their unique environments. Leverage our wide range of capabilities to design, manufacture, and customize nameplates and badging.
Have a Question?
Aluminum Nameplate Finishes and Textures
Aluminum nameplates are one of the most popular nameplate choices because they offer limitless options. Aluminum nameplates incorporate embossing, die-cut shapes, screen or digital printing, and infinite custom textures and finishes. Visit the gallery to get texture and finish ideas for your next aluminum nameplate.
Electroform Nameplate Finishes and Textures
Electroform nameplates feature crisp edges, fine detail and deep relief used with or without colored inks. With nearly endless texture and finishing options, 2D and 3D electroform nameplates are a premier nameplate option for high-end branding. Scroll through the gallery to see just a few of the many 2D and 3D electroform nameplate finishes available.
Nameplates and Badging Product Details
Nameplates and Badging Materials
Boyd recognizes the importance of choosing a material for your custom nameplate that lasts for years. We often use these materials:
- Aluminum: Aluminum nameplates are designed with multiple finishes and are durable and scratch resistant.
- Stainless steel: Stainless steel offers a strong, long-lasting nameplate option combined with multiple treatments and finishes.
- Acrylic: This clear plastic is durable and withstands moderate wear-and-tear.
- Polyester (Mylar): Polyester nameplates are very durable and survive extreme temperatures and chemical environments.
- Polycarbonate (Lexan): Polycarbonate nameplates are heat, water, chemical, and scratch resistant. Polycarbonate is a strong, transparent plastic.
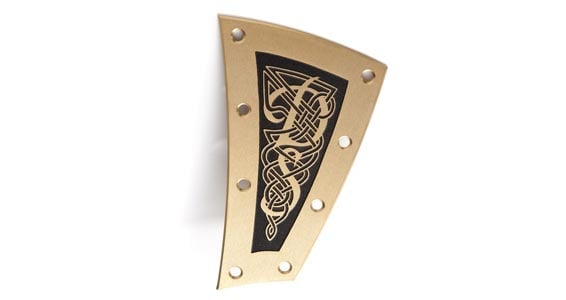
Nameplates and Badging Solutions
We consider every customer’s unique requirements and develop a custom nameplate solution tailored to their needs. Here we list some of our most popular nameplate capabilities, but it is not an exhaustive list. With Boyd, your badging and nameplate options are endless.
Metal nameplates
Combined with three-dimensional detailing and custom inks, metal nameplates create distinct branding. Options include:
- Domed nameplates: Magni-lens technology
- Etched nameplates
- Formed nameplates
- Coined nameplates
- Embossed nameplates
- Metalphoto nameplates
- Diamond carved nameplates
Plated nameplates
Plated nameplates showcase the finest detail to accentuate textures and finishes. Options include:- 2D electroform nameplates
- 3D electroform nameplates
- ElectraGraphic nameplates
Plastic nameplates
A lighter, often more cost-effective option; plastic nameplates are growing in popularity. We have two featured product options that include:- Flat plastic nameplates: Our cost-effective, lightweight, durable and water-and-chemical resistant flat plastic nameplates are made of polycarbonate (Lexan), polyester, and acrylic with the option of screen, digital, or litho-printing. We provide an endless array of colors, halftones, brushed, matte, and different levels of glossy textures.
- Injection-molded plastic nameplates: Our custom injected-molded plastic nameplates are made of polycarbonate (Lexan) and Acrylonitrile Butadiene Styrene (ABS). You can choose engraved plastic and hot or pad stamping. There are many colors and textures available including 3D shapes and custom textures.
Have questions? We’re ready to help!